This is a guest post by Bernd Schreiber, Willem Romanus and Yong Lee, Arthur D. Little
The lean approach, having delivered outstanding performance to companies incorporating it at the center of their corporate transformations, has just about reached the limits of what it can achieve. Digital technologies have become the new focus in many companies, usurping lean and all but causing them to abandon it. However, we don’t believe digital should replace lean. Instead, companies should embrace them both, putting lean at the center of their digital transformations. Recent experience has shown that this can radically simplify the process. It allows companies to identify and apply the most effective levers for the digital journey.
The lean foundation of outstanding organizations
Companies that rely on lean principles achieve relatively high performance levels compared to their competitors. A recent Arthur D. Little automotive study classified the lean lifecycle into three phases and determined annual company growth rates in each phase. Using a key automotive productivity indicator (“hours per vehicle”) as a measure, the correlation with lean implementation was analyzed. (See Figure 1.)
Performance growth of up to 8 percent was common during the Lean Exploitation phase. This decreased as performance improved, and tended to stabilize at around 1 percent in the Lean Excellence phase. Digital technologies have the potential to make a further step-change across all phases.
Technological building blocks according to organizational priorities
Although the advent of these technologies undoubtedly provides huge opportunities and levers for improvement, companies that simply introduce new technological devices and systems, without considering the value stream holistically, run the risk of failure. For example, issues related to deficient value streams and/or poor data quality are seldom overcome by using sophisticated technologies.
Each company needs to configure its own set of technological blocks to address its organizational characteristics and priorities. Five categories of technological building blocks are defined in Arthur D. Little’s digitalization framework, “Future of Operations”. This classification helps companies to trace operational needs to the relevant building block: cognitive, connected, virtual, human centered and value-add.
These building blocks are interconnected, and therefore need a holistic and integrated design approach. They apply across the organization, in both core operational functions such as manufacturing and logistics, and in support functions such as robotics process automation (“RPA”) in production planning and finance. By adopting lean principles, it is much easier to identify the right areas and the levers to make the change. (See Figure 2.)
The full digitalization potential of the value stream
The full digitalization potential of the value stream may be derived using a design approach based on two key questions:
1) Which physical process steps can be automated by mature and proven technologies?
First, design a lean value stream on the greenfield. Simplify the value stream radically by eliminating interfaces through consolidation and integration: make the value-add visible.
For each process step, especially for the non-value-adding ones (“waste”), ask why this step needs to be processed by an employee and by what technology it should be automated. The immediate use of mature technology building blocks on standardized processes will deliver more reliable processes with less failures. Significant increases in productivity are the result of shifting the focus from eliminating waste to creating value-add.
The greenfield value-stream design will differ radically from the current value stream: it reveals its digital potential.
2) Which remaining non-physical (information) process steps can be radically digitalized?
Second, automate and digitalize manual information processing and standard decision-making. Strive for a fully automated target condition in which the employee is just monitoring and confirming automated quality gates. Reduce manual intervention to zero. Especially for high-frequency routines, in which employees transfer data between programs, or even for very complex decisions, robotics process automation, artificial intelligence or decision-supporting systems radically simplify administrative information flows.
Digitalized information flow does not only produce less failures and accelerate workflows significantly, but also creates new value and optimization opportunities through the digital visibility of big data.
A source of future competitive advantage
The ability to effectively and efficiently digitalize an organization’s value stream is a source of future competitive advantage. Identifying and integrating the most appropriate digital technology into the value stream requires a profound understanding of all related business processes, as well as sound understanding of the technologies on offer and their relative maturity.
As with lean management, developing the required capabilities and establishing the necessary mind-set throughout the organization remain top-management issues. The more employees and managers adopt this new lean digital mind-set, the sooner efforts to digitalize will succeed in delivering step changes in business performance.

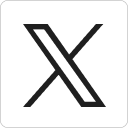



