When we talk about innovation, it’s often accompanied by mention of things such as flatter management structures, more collaborative decision making and transparent flow of information. What probably doesn’t spring to mind is the production line, which to many is the very epitome of the industrial revolution era management style that we’re trying to get away from. Surely that can’t give us any lessons in innovation?
Maybe it’s time to question that stance, as several Chinese companies are using lessons from the production line to engage in what they’re calling accelerated innovation, which attempts to to re-design the innovation process to make it both significantly faster and less expensive.
One of the ways they’re trying to do this is by taking some of the lessons learned from years of making their production lines as efficient as possible, thus cutting lead times, improving the speed of feedback, and reshaping their organizations to make problem solving faster.
The shift has been explored in research published via the Judge Business School this summer. The paper saw over 20 Chinese companies analyzed to understand their approach to innovation. This initial analysis produced a shortlist of companies who went about the task in a particularly novel way and that produced impressive outcomes as a result. The innovators within these companies were then quizzed at length to discover just what it was that they were doing differently.
A shift from the start-up to the industrial behemoth
The traditional language of innovation in the west is of the start-up or skunkworks, beavering away in their garage to swim against the tide of the status quo. Structured processes are generally not seen as being conducive to such an approach.
The approach of the Chinese companies was altogether different. They would typically divide the innovation process up into a number of small steps, each of which would be assigned a small team to work on them. These are then joined together to form an innovation production line.
Re-designing the flow
Central to the speed of innovation in these companies is their willingness to engage in simultaneous engineering, whereby steps within the innovation process are done in parallel to one another. Doing this successfully requires both extremely transparent information and a good degree of co-ordination between the various stages.
This allows a significant improvement upon the launch-test-improve process that so many innovations go through. This rapid iteration process allows products and processes to be constantly improved due to the speed with which both feedback can be received and changes implemented based upon these suggestions. This approach advocates launching products that are good enough, and then using feedback to make them better.
This feature was prevalent in all of the truly innovative companies studied in China, and it allowed many to have a very short time to market for new products and services. At the heart of the philosophy was one of marginal gains. Each improvement in isolation may be small, but when taken collectively they added up to something considerable.
Accelerated decision making
The research revealed that most of the innovative Chinese companies would have quite a rigid vertical hierarchy, in that bosses would set clearly defined goals, budgets and deadlines. These would then be cascaded down through the organization. Once there however, employees would enjoy considerable horizontal freedom, which allowed the rapid flow if information and resources between departments and functions. For instance, problems in one department would often be tackled by people from throughout the company, with a collaborative approach taken to ensure things get done.
So whilst goals are rigid, how teams go about achieving them are much more flexible. Suffice to say, this approach relies upon the sound judgement of the executive, but it also provides a speed of action that can be very useful. Employees in the Chinese companies complained that achieving consensus in western companies would often take much longer, thus slowing down innovation considerably.
The study concludes that whilst this approach may not offer industry changing innovations per se, it does facilitate the kind of rapid followership model that companies such as Apple and Zara have deployed so successfully in their respective fields.

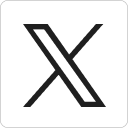




Interesting. I'd never thought that China could really tell us much about innovation. I might have to reassess.