I wrote recently about the way knowledge can rapidly drain out of an organization as people retire, and the importance of trying to capture that knowledge long before they do so.
A recent paper, authored by researchers from the University of Illinois, highlights just how pernicious this knowledge drain can be to the performance of an organization.
They highlight how this can be especially pertinent when those improvements are designed to filter through the supply chain.
“The issue is one that we have seen many times, in that firms try to implement improvements with suppliers, and then that initial improvement begins to slowly degrade again,” the authors say. “It turns out there is a systematic reason for it, and it’s the depreciation of organizational knowledge.”
The study explores how the depreciation of organizational knowledge impacts these efforts.
Over 2,700 quality improvement efforts were analyzed across nearly 300 manufacturers. The analysis revealed that such ‘organizational forgetting’ reduced the gains obtained by the efforts by around 29 percent.
“We find that quality competence gained through production experience is degraded over time by organizational forgetting,” the authors say. “In addition, we find that even when buyers work with suppliers to improve suppliers’ quality, such ‘induced learning’ also is subject to depreciation. Overall, our findings suggest that when firms employ process improvement initiatives to address critical quality issues, they must revisit them to periodically ensure that the improvement is sustained.”
The problem was one that was found to be universal and not a consequence of a particular culture or management style.
“The development and depreciation of knowledge within organizations are processes that occur concurrently in all firms, in just about all industries,” they say. “It’s not something that’s just concentrated in a few firms. It’s something that is general and likely to happen in most scenarios that involve supply chains or a complex industrial environment.”
They go on to suggest that a big part of the problem is that the improvements that are gained through process improvement initiatives are often not particularly consistent over time.
“When you teach someone something, or if this person is learning on the job, the arrow does not continually point up,” they explain. “It’s going to come down, so you have to correct course every so often, because as you are learning, you also are slowly forgetting. And that’s what you have to be careful about. Fixing the problem is important, but occasionally revisiting the fix is equally as important.”
This is compounded by the rapid change in technology or indeed the demands of the market, which so often require new processes to be learned, thus invalidating what has gone before. Quality improvement is not, therefore, something that you can do once and forget, but rather an ongoing challenge.
This challenge is thus compounded by any leakage of knowledge, and the authors implore managers to appreciate that improvements in quality are not going to be retained indefinitely, and therefore there needs to be a culture of continuous improvement for things to work well in the long-term.

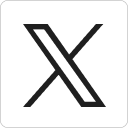




Makes sense. I'm not sure knowledge management ever really took off, for all the hype around it in the 80's and 90's