The so called materials genome has been a hot topic since the Whitehouse launched the Materials Genome Initiative in 2011, which was designed to aid the deployment of advanced materials.
I’ve looked at a number of applications of this, from the paper by the University of Alabama that explored how we can detect degradation of machinery before it breaks, to a German start-up that are taking this thinking out of the lab and onto our railways. Both projects utilized the vibration patterns of machines to detect patterns that signify degradation.
Understanding materials
Gaining a better understanding of just how materials function is the mission of New York based Sentient Science. The company have been working with NASA to collate data on the performance of the kind of materials they use in their machines. They’re looking to feed this data into a new product, called DigitalClone, which aims to predict the lifespan of any machine.
The company tested the software out on a unique spur gear that has a long and clearly documented performance history. The device, which is used in helicopter drive trains has around 25 years worth of data that can be tested against. Having this kind of data to test the system on is invaluable as companies don’t often release performance data.
The system works by creating a clone of the component, and uses its knowledge of the physics of lubrication, wear and friction to make a prediction about the lifespan of the component.
Testing the metal
A digital model was then created of the gear to compare the predictions made with the actual performance of the gear over the past few decades.
Thankfully, the comparison proved a perfect match, suggesting that the algorithms were exceptionally good at understanding material behavior.
It was further tested via 11 more tests at companies such as General Electric and Boeing, with field testing being undertaken via its DigitalClone Live product, which installs sensors into gearboxes and then uses the live data collected to predict both device performance and prospects for failure.
“Instead of running physical tests for a year and getting three test points, we can give you thousands of test points in days,” they say. “You will have the world’s most tested products, which will run in the field at the lowest cost to operate.”
This has enabled existing clients to make significant savings. For instance, a wind energy client has managed to reduce the price of wind energy from 11 cents per kilowatt hour to 3.5 cents, with the team confident that such savings will eventually make renewable energy economically viable.
It seems inevitable that as we gain greater understanding of the materials that make up our mechanical landscape that such savings will spread. Whilst the materials genome project has not gained the publicity of its human genome alternative, these initial results suggest that should be a situation that needs to change.

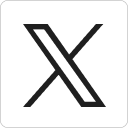



