Retrofitting an assembly line whenever you change the model of car you wish to build can be a complex and time-consuming process. An interesting project is attempting to use 3D scanning to improve our understanding of the process.
The project began as the car industry has been gradually increasing the range and number of models they produce. Whereas in the 50s, companies would perhaps manufacture a couple of models per plant, there are now infinitely more models made by most companies. At Volkswagen, for instance, when buses, trucks and motorbikes are included, they make around 300 different models.
Obviously having multiple assembly lines for each model is impractical, so the industry is moving towards having a single assembly line that adapts to each model change.
“This would require increased flexibility in production, more robots and a higher level of digitisation,” the researchers say.
Flexible manufacturing
The research team are helping to achieve this by working within the Virtual Technologies of Corporate Research group at Volkswagen, where the production lines are digitized in preparation for a change in model. The team helped this process by 3D scanning the production line during live operations, with this data then used to generate a 3D layout of the production facility, which in turn can be used in simulations of how it will change to manufacture each new model.
The system is vital because the construction plans plants typically have are usually made redundant by the constant changes that are made. This need for adaptability would often result in plants constructing models out of polystyrene. Whilst the virtual models can therefore take a little while to produce, they are more accurate and timely than previous methods. It also allows previously hard to reach areas to be accurately mapped.
The team were hired by VW for the launch of their Tiguan and Crafter models, with the process revealing some significant alterations to the production halls to allow assembly to take place.
A data challenge
Such is the efficiency of scanning technologies, the researchers believe that the scan itself is relatively straightforward, with the evaluation of the data generated the tricky part. The team hope to overcome this by automating as much of the data analysis as possible, and they are working on the software required for this task at the moment.
It’s an interesting project and one that highlights some of the technological progress being made in the way cars are made.

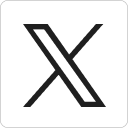



