Whilst the most visible autonomous transportation projects have undoubtedly been the driverless cars developed by companies such as Waymo, the technology is also being used in less glamorous ways. For instance, I wrote recently about the work of Swedish company Semcon, who have developed technology to allow cars to drive themselves off the production line, into the shipping area and all of the various other stages of the logistics process.
Or you’ve got the European consortium behind the Iliad Project, which is working on the development of autonomous forklift trucks. The team, which consists of robotics specialists from the UK, Sweden, Italy and Germany, have been working on the project for four years and believe the machines can support tasks such as packing, palletising and transporting goods.
Slotting smoothly in
The team believe that ILIAD will prove a valuable addition to the warehouse environment because it’s an easy and low-cost deployment that won’t require significant infrastructure investments. What’s more, the robot is ‘human aware’, using AI and computer vision to monitor the movement of humans in the vicinity.
This AI engine also empowers ILIAD with the ability to learn and improve over time from the data it collects as it goes about its work. This gives the potential to scale the system and easily add (or remove) robots from the fleet at any time.
The ultimate aim is to develop a robot capable of slotting into the logistics operations in various industries. During the development stage however, it is primarily being tested in the fresh food sector. This industry was chosen because of the challenging requirements posed by short shelf life products, the high cost of wastage, extreme time pressures to respond to market needs and the demand for traceability.
“Our goal is to deliver an economical, flexible robotic solution that can be easily deployed and integrated into current warehouse facilities and which guarantees efficient and safe operation in environments shared with humans,” the team say. “The project will push the state-of-the-art in human-robot interaction, overcoming persistent barriers to greater adoption of automation in logistics operations in many industries, starting with the food sector.”
The researchers hope to reduce the capital costs involved in the deployment of the robots by ensuring that they’re both self-deploying and self-optimizing. They also hope to clearly demonstrate how safe they are when working alongside human co-workers in complex warehouse environments.
“The massive scale of food volumes moved by the sector means that being able to do this quickly and efficiently can make the difference between business success or failure,” they conclude. “Movement costs “per pallet” and “per case” are tracked as Key Performance Indicators in most warehousing and distribution operations. Robots seamlessly integrating alongside humans, often working collaboratively, will unlock significant productivity advances in the sector while also serving to help address anticipated challenges resulting from increased competition and escalating operating costs over the coming years.”
We’ve seen a significant increase in the level of automation in warehousing and logistics processes in recent years, and this is another example of the direction the industry is going in.

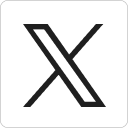



