Most technological ages have come complete with a panoply of buzzwords that often befuddle as much as untangle the topics they describe. The 4th Industrial Revolution, coined by the World Economic Forum’s Klaus Schwab a few years ago, is no exception. One of the more interesting buzzwords within this is Industry 4.0, with supporters claiming that the emergence of powerful computing and AI-based technologies will transform industrial processes.
As with many kinds of digital transformation, the expectations are significant for Industry 4.0, but a lack of real understanding of the term is a key barrier to adoption.
A recent survey by PwC found that many exponents of Industry 4.0 expect to see gains such as revenue increases, improved efficiency savings and customer engagement. However, 60% of respondents said they were only dabbling with these technologies, with just 3% saying they had achieved anything close to the working definition of Industry 4.0.
In order for companies to transform their industrial processes with disruptive technologies, they first need to understand what those technologies are capable of, how they will impact the existing ecosystem and what benefits they will bring.
Toby Olshanetsky, CEO of proof-of-concept solution prooV, says the real challenge to achieving Industry 4.0 lies in this process of testing and evaluating technologies.
“Companies are drawn to the endgame of Industry 4.0,” Olshanetsky said. “They are drawn to the advantages it will bring to their manufacturing processes and to their businesses as a whole. But what many enterprises are missing is an accessible way to make that innovation happen.”
Industry 4.0 was first proposed in Germany in 2011, and purports to propel us into a new way of thinking about industry. It contains things such as the smart factory and cyber-physical monitoring systems, and broadly follows these four principles:
- Transparent information – it is vital that a virtual copy of the physical world can be created, and this can only be done if data is freely available, from raw sensor data attached to machines all the way up to higher-value contextual information
- Interoperability of components – the Internet of Things (IoT) underpins Industry 4.0, and allows for the various machines, devices and sensors to communicate effectively with one another.
- Technical assistance – technology should not be invested in just for the sake of it, but rather because it provides clear assistance to humans, either in doing their job or making informed decisions.
- Decentralized decisions – by making information more transparent and readily available, it should move the decision making process closer to the point of action, with only exceptional decisions escalated up the hierarchy.
Getting started
As a previous post highlighted, it’s rare to find a sector where digital transformation has come easy, with many companies getting stuck in the proof-of-concept phase where restrictions, regulations and risks keep them from scaling up their innovations into something truly transformative.
With Industry 4.0, even among those who believe in its potential, there is little real clarity around what it means and how companies can get started.
As with other instances of digital transformation, the problem is seldom one of technology, but more one of social and cultural change. I’ve written before about the importance of re-engineering jobs before we can begin to make headway with artificial intelligence, and similar hurdles exist for Industry 4.0 adoption. While there is no cookbook and recipe for success, there are nonetheless a few things you can do to help you get started.
- Understand what you want to achieve – and this doesn’t mean in terms of investing in technology, but rather what are the business outcomes and measurements that matter most to your business. These drive everything else.
- Run proof-of-concepts – When you know what business outcomes and measurements you want, you know what kinds of technologies you need to test and how you want to evaluate them. In large parts, you won’t know which solution will best improve your existing processes and meet your company’s innovation needs, but you will know what you are looking for. So the best way is to experiment as much as you can. Create a culture of experimentation where you are constantly testing your assumptions with tailored proof-of-concepts.
“The most important part of running proof-of-concepts is testing technologies in a setting that reflects your actual production environment, especially when innovating in a new arena like Industry 4.0,” Olshanetsky said. “That way, you know that the results you get and the decisions you make are specifically relevant to your company’s technological challenges, needs and goals.”
- Build on success stories – too often pilots and proof-of-concepts are considered safe ways to appear to be innovating without disrupting the status quo. To truly change, you will need to use the success stories that emerge from your experiments to scale them up. Success stories are those technologies that showed in your proof-of-concept that they are compatible with your company’s infrastructure and measure up to the business objectives you defined.
- Visualize results and craft stories – the best way to communicate these successes is via stories and visual displays. Use these both to highlight organizational deficiencies and also to promote successful solutions.
- Take a data-driven approach – every organization will have power bases, and these can often stop innovation if it threatens departments or approaches that are dear to powerful executives. To overcome this, take a data-driven approach to operational change so that proof and outcomes take priority.
It probably goes without saying that no form of transformation is easy, and digital transformation is no exception. Indeed, with many technologies entering the market independently of initiatives such as Industry 4.0, it can be tempting to wonder if it’s all worth the hassle.
In the long term however, Industry 4.0 is likely to be fundamental to giving companies the platform through which they can build, adapt and thrive in the modern economy. It’s no surprise that the German government has thrown its weight behind Industry 4.0 at both a national and regional level to ensure that the skills required are present across the economy. It’s a process that is helping to make manufacturing sexy again as companies battle with tech giants for the best talent.
“One consequence is that many talented young people, far more than today, are keen to work in industrial production again,” says ETH Zurich’s Paul Schönsleben in a recently published paper. “In that respect, Industry 4.0 is above all an investment in the long-term future of production locations in high-wage countries.”
Whether for individual corporates, or society as a whole, the importance of initiatives such as Industry 4.0 cannot therefore be brushed aside as another passing technological fad. If companies adopt the right long-term strategy they can ensure they’re on the right side of this transformation, and hopefully these tips will help get you off on the right foot.

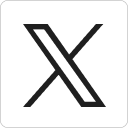



