The tremendous importance of the work that is undertaken in hospital operating rooms would perhaps lend one to think the work is optimized to within an inch of its life. Alas, new research from Michigan State University highlights just how inefficient it often is.
For instance, the paper highlights how unplanned supplies can add up to 10 minutes to each surgical procedure, and better planning could save around $1,800 each time, which equates to a whopping $28 million per year.
“This problem is due to the fact that quality of care has always taken precedence over cost—and rightly so,” the researchers say. “However, with increasing pressure on health care organizations, they are trying to find ways to jointly increase quality and reduce costs.”
Unplanned costs
The research suggests that these unplanned costs not only add to the expenditure of the unit, but also put patient safety at risk. The researchers observed hospital operating rooms for several hundred hours to examine how they function. They found that a fundamental lack of standardization was a major issue, especially in the planning process.
“In most hospitals, every surgeon is allowed to make their own decisions in terms of equipment and supplies,” the researchers explain. “Surgeons are comfortable using certain supplies due to their past experiences; this increases the variance among items and the number of items that hospitals need to carry in inventory.”
Equipment and supplies are requested by surgeons via a physician preference card, with this system typically resulted in personalized requests for each individual surgeon rather than a standardized process. The researchers believe that as a result of this, shortages are typically addressed in real-time, which reduces the quality of surgery while also increasing costs.
“If a doctor doesn’t have what they immediately need, a surgical team member must find it, which becomes an unplanned cost—and potentially a health risk if they leave the area,” the researchers explain. “On the other hand, if a surgeon requests something that isn’t necessary for the surgery, it’s simply a waste of money.”
The analysis found that it’s also common for surgeons to err on the side of caution and bring an excess of supplies for every eventuality. This can save time, but the researchers believe a more standardized approach could reduce redundancies and save considerable time and money.
Despite the changes appearing minor, they can add up to significant cost savings over the course of a year. This was just one issue identified by the researchers, and they urge hospital managers to do more of this kind of exercise to try and uncover similar issues they can address.
Communication challenges
For instance, the team also identified issues around the way communication occurs among surgical teams. The high turnover of personnel within teams makes it difficult to communicate effectively, with the issues around inventory an indicator of this.
“Our research should encourage hospitals to embrace systems that can better track unplanned costs and plan ahead,” the researchers explain. “Hospitals should explore methods to incentivize surgeons to plan more often. This may be achieved by providing visibility about unplanned costs and workarounds, offering greater control on administering supplies, and rewarding for unplanned cost reduction.”
In the fast-paced nature of hospital work, such improvements can often be difficult to make as staff have so little slack to make them, but the research reminds us of the benefits that can accrue if they can find that time.

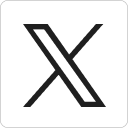



