Absence from work is a widespread issue in Latin America and Asia, with as much as 10 percent of a business’s workforce potentially failing to show up on any given day. This prevalent risk introduces significant uncertainty, particularly for businesses operating on thin profit margins, according to research from Harvard Business School.
While examining a factory in India, researchers discovered a pragmatic approach for maintaining productivity amidst regular employee absenteeism: fostering strong inter-managerial relationships to facilitate borrowing of employees from other departments to cover for absentees.
Staying on track
The study delved into the strategies employed by managers to cope with high rates of absenteeism, focusing on a ready-made garment factory in India. Despite operating with tight schedules across some 20 production lines, each with 60 workers, the factory faced an average daily absenteeism rate of 11 percent. On any given day, at least one production line experienced an absence rate of 20 percent or more.
Absenteeism wasn’t solely due to sickness; it also stemmed from cultural festivals celebrated by factory workers hailing from diverse rural backgrounds across the country. These festivals, varying based on cultural and religious affiliations, further complicated absenteeism prediction.
The company’s CEO previously attempted to address the chronic absenteeism issue by enlisting the help of a prominent consultant, who endeavored to establish a formal system for reallocating workers among lines based on demand, albeit unsuccessfully. Given the daily fluctuations in attendance, it required considerable time and effort—half a shift—to thoroughly analyze the problem and implement solutions.
Coping strategies
To assess managerial coping strategies, the researchers devised an ingenious tracking system for workers in the factory. At each station, they installed tables where employees would sign in and out for their shifts. Through this method, researchers observed that managers established informal arrangements with neighboring managers to facilitate lending and borrowing of workers as necessary.
By promptly gauging the number of absent employees in their department each morning, managers could swiftly enlist assistance from neighboring departments, particularly when facing deadlines for significant orders. Implicit in these arrangements was the understanding that assistance would be reciprocated when needed.
The research suggests that rather than relying on a central system to replace workers, it might be more effective to encourage managers to make handshake agreements to share employees. This could help fill needed jobs on production lines, where different tasks require different skills.
Using a mathematical model, the researchers found that having about seven or eight connections among managers could increase productivity by 1.3 percent. This might not seem like much, but for a company dealing with lots of absent workers, it could make a real difference.
The researchers advised the CEO of the factory to encourage senior managers to build relationships not only with those nearby, but also with colleagues in other parts of the factory. This could help create a more flexible and efficient workforce.

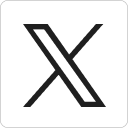



