Last year I wrote about a report published by the logistics company DHL where they argued the benefits of collaborating with your competitors on supply chain and logistical issues. The collaboration they talk about is not just confined to the usual innovation related topics, but on sharing warehousing space or transport networks. They cite the example of French retailer Carrefour sharing warehousing space with other retailers.
DHL have found a friend in their mission in the shape of new research published by the University of Illinois. The research, split across two papers, argues that a lack of collaboration between big players at either end of the supply chain is preventing companies from gaining efficiencies in a whole host of areas.
“There’s more power at the end of supply chains, and we found that not talking to the firm that provides your suppliers with their raw materials is not very helpful,” the researchers said. “We think that there’s a lot of efficiency to be gained there.”
If you’re an automobile company, you’re buying parts that contain steel and aluminum from small suppliers, who, in turn, buy these raw materials from another firm. And these main suppliers of raw materials, whether it’s raw aluminum or raw steel, are fewer and as big, if not bigger, than the automotive firms – “as big as Ford or GM, but on the other side of the supply line,” they continued.
“But we find that most companies focused on producing cars and trucks don’t have open lines of communication with the firms that produce steel or aluminum,” they went on. “They only talk to the middle men, the suppliers. The auto firms believe they should only focus on what they do best, and that it’s incumbent upon their suppliers to talk to the raw material supplier.”
All of which is rather short-sighted. Just as in the DHL report, the papers advocate significantly greater collaboration between firms throughout the supply chain, and in particular the creation of a sourcing hub at the centre through which collaborations can occur.
“It’s a place where the buyer and suppliers can come together and evaluate what, exactly, is good for everybody,” it says. “The idea is powerful and simple and seems to make a lot of sense on its face, but for the most part, it hasn’t happened yet.”
The bulk of the report surrounds using the collaboration hub within industries that consume a lot of raw materials, such as car manufacturing, but as the DHL report earlier highlights, such collaboration can equally be used by any industry with a considerable supply chain or logistical operation.

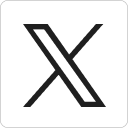




Collaboration with competitors makes sense when the services and product are not unique or when one cannot create a differentiating strategy leading to competitive advantage. That may be true of most of what companies wish to get from Logistics Partners, but I have had several opportunities to collaborate with one partner in ways that I did not want to share with other competitors, and which led to distinct outperformance for some time. Knowing when to collaborate, and when not-to is a critical supply chain management skill.