The football World Cup is approaching a conclusion at the moment, and fans from around the world will be tuning in to see which team comes out on top and claims the crown as the best in the world. During the month of competition in Brazil, there have undoubtedly been numerous posts and articles relating how lessons from the pitch can translate into corporate life.
Few perhaps, have used the ball itself as the key protagonist however. Researchers from the School of International and Public Affairs however, believe that a study of footballs can increase our understanding of how innovative technologies are adopted.
They delved into the ball manufacturing industry in Pakistan, where it’s estimated 40% of the global supply of footballs are made. The traditional football is stitched together using 12 pentagons and 20 hexagons. This design produces some manufacturing wastage however, as pentagons can’t be cut from a rectangular sheet without producing waste material.
The research team devised a method of producing balls with less waste and presented their approach to a randomly selected sample of 35 manufacturers in the industry (out of 135). The new approach would increase the number of pentagons that could be cut from a sheet from 256 to 272. Despite the apparently straightforward savings, just 5 of the 35 companies applied the approach.
“We thought the firms we gave the die would adopt it quickly and our research would focus on the spread of the technology to other firms in Sialkot,” the researchers say. “It was very surprising to find that very few of the firms receiving the die were using it for production.”
Such lacklustre adoption of seemingly obvious improvements is perhaps not surprising to any readers that have tried to implement innovations within traditional industries. The researchers suggested that the root cause of the failure was a misalignment of incentives. They believe that cutters were disinclined to take up the innovation because learning the new technique would take time, which would result in fewer balls being made initially, and therefore less money for them.
“Companies may have to change the way they pay workers in order for innovations to be adopted,” the researchers say. “If workers don’t expect to gain from adoption of new technologies, they won’t support them and firms will be less innovative. Without changes, firms will continue to leave money on the table.”
To test their hypothesis, the researchers attempted to ‘sell’ the innovation to a fresh group of companies, but this time offered employees a lump sum payment rather than the traditional piece rate. In this instance, take-up of the innovation rose to around 50%.
It’s probably fair to say that the findings aren’t altogether replicable into other industries, but they do nonetheless remind us that we need to think about how innovations will effect those charged with utilizing them if we want them to be implemented.

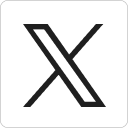



