Recently I attended a talk delivered to guests of the UK and India Business Council from Dr Devi Shetty, the famous Indian heart surgeon who has been dubbed the Henry Ford of Healthcare for his work on using production line methods to reduce the cost of healthcare to a pittance, whilst maintaining good standards of care.
It’s an approach that’s vindicated by a recent study highlighting how lean approaches can help to cut waiting times in accident and emergency (A&E) departments.
The report highlights how lessons from manufacturing based methodologies such as lean and six sigma can translate well to the healthcare world, helping to tackle the immense strain that many emergency wards find themselves under.
The Australian study analyzed the implementation of lean six sigma in a large hospital in Melbourne to gauge how effective it was at reducing the time taken to both assess and stabilize patients in A&E.
The team were also keen to learn how effective it was at improving the flow of patients through the hospital, all the way from their admission through to their discharge back into the community.
It emerged that success or failure often rested on the ability of the department to balance conflicting flows and therefore ensure the smooth operation of the unit and limit any stress related to the process for patients and their loved ones.
“In recent years hospitals have been trying to adapt LSS processes to streamline processes and improve costs,” the authors say.
“There have been earlier claims about work intensification experienced by employees in lean manufacturing. Therefore, we studied the outcomes after transferring LSS concepts into a hospital context, to streamline processes and improve costs there,” they continue.
As I mentioned in the post about the Devi Shetty talk however, there are often challenges between knowing something might work and actually implementing it, and the paper revealed the differences between implementing lean in healthcare compared to manufacturing.
Nevertheless, they were fervent in their support for lean six sigma as a means of improving patient flow within A&E. It also allowed the hospital to free up more beds, which coupled with new monitoring software to assess bed availability helped matters enormously.
At a ward level, it resulted in more rehabilitation beds becoming available, which in turn enhanced the discharge process, which further improved the flow of patients.
As with most change projects however, the authors reveal that implementation is often incredibly difficult and a change towards a leaner approach to operations can take some time and are fraught with risk.
The following talk outlines some of the steps you can take if you’re undergoing a lean transformation yourself. It features Dan Jones, chairman of the Lean Enterprise Academy.
He talks about things such as:
- Developing and rethinking successful products and services.
- Developing the end-to-end process.
- Understanding the work that creates value for the customer in order to stabilize, standardize and practice improvement.
- Learn to manage by seeing the whole, setting direction and focusing on the vital few business issues and develop people through coaching and mentoring.
- Ask the right questions – to find out about what we don’t know.

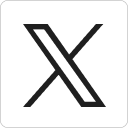




Like with most of these things, the implementation is key. I mean lean has been around for ages, it's not a new concept.