It’s increasingly common for the things we use to monitor their own health and attempt corrective action before things get too bad. For instance, I wrote recently about a report in the future of housing that suggested our homes will eventually have this capability.
A recent paper from the University of Alabama in Huntsville describes a new algorithm that aims to provide a similar diagnostic function for the mechanical systems that form such a big part of our commercial engine.
Automated diagnostics
“The ability to extract dependable and actionable information from the vibration of machines will allow businesses to keep their assets running for longer while spending far less in maintenance. Also, the investment to get there will be just software,” the researcher says.
The algorithm was tested using data from both real-life and unpredictable situations, and it was able to diagnose the situation with an accuracy of around 90%.
“This technology is in the trial stage. We are seeing how it performs in the field. If the results so far hold, we will build credibility and hopefully gain acceptance with our Dept. of Defense partners,” he continues. “At the same time, we are expanding our client base to include the private sector. There, we believe we will have an even larger impact in the way they do business.”
Machine diagnostics typically involves a form of vibration analysis that is looking for anomalies in how the machines and gearboxes move. This change in vibration can be an accurate sign of wear and tear, and indicates that maintenance is required.
“Any machine shakes and vibrates, and it will vibrate a little differently when there is something wrong, like a fault,” the researcher says. “If you can detect a fault before it becomes serious, then you can plan ahead and reduce the time machinery spends idle in the shop. As we all know, time is money.”
Getting the information
A major challenge with this is securing the information required to make the right call, especially in often noisy environments where it can be difficult to differentiate sounds.
Existing algorithms tend to assume that most vibrations are static, and therefore that signal and noise can be differentiated by frequency. Whilst a nice theory in an ideal world, this seldom holds true in reality.
So the new algorithm has been taught the basic principles of physics that enable it to determine faults in a vibrating environment.
It has already been used in the US Air Force to help with their helicopter maintenance, and they are very happy with the initial results.
“His approach, using machine learning, permits the analysis to look at the history of the data output rather than just a single flight. We train the algorithm much like you train your cell phone to understand your voice,” they say. “When the particular component we are monitoring sees vibration signatures that no longer reflect the normal performance of a component, an alert is passed to the maintenance team.”
It will be interesting to see if this manages to be rolled out in a wider range of environments.
If you like this post, consider buying me a coffee

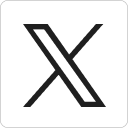



