Ever since Sir David Attenborough brought the environmental crisis caused by plastic waste to global attention, it’s been an issue on everyone’s lips. Whilst various projects have attempted to rectify matters, whether through smarter packaging, using less materials in packaging, or by being better able to sort and recycle the waste we do produce, the problem has yet to be solved in any meaningful way.
Part of the challenge is the sheer volume of waste that needs to be sorted through, often manually, by workers sifting through an estimated 68 million tons of recycling per year. The job is dirty, unsafe and deadly dull, and so it’s perhaps not surprising that mistakes are made.
Whilst on the surface, the work is not especially difficult, it’s one of those tasks that humans are intuitively great at, but that machines have long struggled to master. If you think of each time you pick up an object, you can instantly identify its many qualities, from its texture to its weight, its size to its shape. In an instant we can calculate how best to handle the object based upon this insight.
Programming a machine to do this is incredibly difficult, as hard robot hands lack the dexterity with which human hands perform, and soft, rubbery hands that have the required dexterity are prone to malfunctioning. As such, providing robotic assistance to waste managers has been slow in coming.
Help may be trundling over the horizon however. A team from MIT’s Computer Science and Artificial Intelligence Lab (CSAIL), together with help from Amazon, JD, the Toyota Research Institute and the National Science Foundation, have developed a robotic system that aims to automate the job of sorting waste for recycling. It’s capable of sifting through trash and determining whether it’s paper, metal or plastic.
Robotic recycling
The ‘RoCycle’ system comes with a teflon hand with sensors in the fingertips to assess each object it encounters for its size and stiffness. When put through its paces, it was found to be 85% accurate at detecting stationary objects, and 63% accurate when assessing them on a moving conveyor belt.
“Our robot’s sensorized skin provides haptic feedback that allows it to differentiate between a wide range of objects, from the rigid to the squishy,” the team say. “Computer vision alone will not be able to solve the problem of giving machines human-like perception, so being able to use tactile input is of vital importance.”
The team believe that it’s vital that pure sight-based sorting is moved beyond, as something as commonplace as a coffee cup could look similar on the surface, but be made of completely different materials.
Smart sensing
RoCycle features a motor-driven hand made of a new material known as ‘auxetics’. Auxetics is unique in that whereas most materials tend to get narrower when they’re pulled on, auxetics gets wider. The MIT team used this capability to create a material that twists to either the left or the right when it’s cut. This allows them to create a ‘left hand’ and ‘right hand’ for the robot that are capable of both interlocking and opposing each other’s rotation. The team believe this enables the robot to have a wider range of movement.
“In contrast to soft robots, whose fluid-driven approach requires air pumps and compressors, this approach combines twisting with extension, meaning that you’re able to use regular motors,” they explain.
It is also equipped with what the team call a ‘strain sensor’, which is used to estimate the size of any object the robot encounters. Two pressure sensors then gauge the force required to successfully grasp the object. The data from these is then combined with a database of the size and stiffness of objects to instruct the robot on the kind of material the object is made of.
“In other words, we estimate the size and measure the pressure difference between the current closed hand and what a normal open hand should look like,” the team explain. “We use this pressure difference and size to classify the specific object based on information about different objects that we’ve already measured.”
Automating waste management
RoCycle is part of a wider body of work that is attempting to bring automation into the waste management sector. A few years ago a Swedish team developed a robot, called ROAR (or robot-based autonomous refuse handling), which was capable of working alongside the refuse truck, collecting bins from the street, delivering them to the vehicle and then dumping the contents inside.
Such a device was primarily designed to remove much of the heavy lifting involved in refuse management, but it’s not beyond the imagination to see such machines eventually sorting the rubbish that they collect as well.
These kind of innovations are sorely needed in a sector that remains largely manual. If countries are serious about the waste management problems they face, then innovation is something that is vital to the efficient and effective processing of waste materials, and hopefully their re-entry and re-use in the supply chain.
“If a system like RoCycle could be deployed on a wide scale, we’d potentially be able to have the convenience of single-stream recycling with the lower contamination rates of multi-stream recycling,” the MIT team explain.
It perhaps goes without saying that the technology is still some way from market ready, and the team plan to further develop the technology so that it can incorporate live video footage of the waste objects to help inform the machine’s decision making. The team believe this can bolster the accuracy of the technology, whilst even allowing it to better identify a wider range of materials. They are nonetheless confident that RoCycle, and machines like it, can play a big part in the future of waste management.
Check out the video below to see the RoCycle in action.

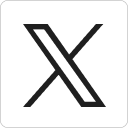



